Boiling in Microchannels: integrated design of closed-loop cooling system for devices operating at high heat fluxes
Find Similar History 22 Claim Ownership Request Data Change Add FavouriteTitle
CoPED ID
Status
Value
Start Date
End Date
Description
Current developments and future trends in small-scale devices used in a variety of industries such as electronic equipment and micro-process and refrigeration systems, place an increasing demand for removing higher thermal loads from small areas. In some cases further developments are simply not possible unless the problem of providing adequate cooling is resolved. The progression from air to liquid and specifically flow boiling to transfer the high heat fluxes generated is thus the only possible way forward. Evaporative cooling can, not only transfer these loads but also offer greater temperature uniformity since the working fluid can be (in a carefully designed system) at a constant saturation temperature. The consideration of microchannel flow boiling processes has been made possible by developments in microfabrication techniques both in metals and substances such as silicon. However, there still remain fundamental fluid flow and heat transfer related questions that need to be addressed before a wider use of these micro heat exchangers is possible in industry. The specific challenges that will be researched - both fundamental and practical in nature - include flow instabilities and mal-distribution which are the result of interaction between the system manifolds and the external circuit. These can lead to flow reversal and dry-out in the heat exchanger with subsequent drastic reduction in heat transfer rates. The understanding of the fundamental physical phenomena and their relevance to industrial designs is one of the focal points and constitutes one of the major challenges of the proposed research. The effect of other parameters such as inlet sub-cooling, which again relates not only to the micro-heat exchanger itself but also to the overall design, will be addressed along with material/surface characteristics through the use of both metallic and silicon microchannels.
The work proposed will include carefully contacted detailed experiments measuring relevant parameters such as local heat flux, temperature and pressure combined with flow visualization through industrially available and purposely developed and manufactured sensors. The research teams will not only develop or adapt advanced instruments for accurate measurements at these small scales but also develop new three-dimensional numerical tools capable of capturing the extremely complex physical phenomena at, for example the triple-line (vapour-liquid-solid). These techniques will not only help elucidate the current phenomena but can find wide application in similar research, both in thermal and biomedical flows.
The proposal brings together two teams of academics working both in microfabrication/sensors and two-phase flow supported by industry (Thermacore, Selex Galileo, Sustainable Engine Systems and Rainford Precision) to tackle some of the key fundamental challenges that will enable a wider adoption of this cooling method hence meeting current and future needs in the industry. The proposed research will also have a wider impact on energy conservation and environmental footprint trough, for example, more efficient thermal management of data/supercomputing centres around the world that can lead to a reduction in energy consumption and reuse of heat that would otherwise be rejected.
More Information
Potential Impact:
A range of cooling techniques has already been considered for cooling devices operating at fluxes above 0.5 MW/m2, the practical limit for air cooling, such as liquid convection, pool boiling, liquid jet impingement or sprays, heat pipes or capillary pumped loops, thermo-acoustic refrigeration and thermoelectric devices. None has reached a state of commercial maturity and many technological difficulties still arise at heat fluxes above 1 MW/m2. Heat sinks comprising many microchannels in parallel, connected by manifolds, offer the advantage of a high ratio of heat transfer area to base area in contact with the heat source. Evaporative cooling offers the prospect of much higher heat fluxes, due to the higher heat transfer coefficients associated with bubble formation and growth in microchannels, and greater regulation and uniformity of temperature because the coolant is at its saturation temperature.
The research groups at BU and UoE have long-term experience in heat transfer at the microscale and have worked together before in this area. The access to high quality micromachining and microfabrication facilities, including clean room facilities, permits integrated production of cooling systems and microelectronic devices. The links with Thermacore, who are specialists in advanced cooling technologies, Sustainable Engine Systems (SES) who specialise in extremely high surface/volume ratio heat exchangers and Selex, who use advanced cooling systems, provides the research partnership with avenues for exploitation of their research outcomes. This project will open up a range of applications in enhanced thermal control of power plants, cooling of electronics, heat pipes for space and earth applications, chemical micro-reactors, micro-heaters and refrigeration devices and thermal control for biological detection devices. The possible use of manifold designs developed in this project with Selective Laser Melting micro-heat exchangers (SES) in applications such as heat engines is also an important opportunity. In some of the application areas above, the proposed research developments will allow step changes in thermal processes and facilitate or enable new designs and product development and in some others, benefits such as lightness and compactness, rapid heat and mass transport, extremely precise control of the process conditions, high performance (i.e. high throughput per unit hardware volume), cost economies through mass production and availability for distributed or mobile applications.
The UK currently has a commercial presence in the production of power electronics and in providing thermal solutions for power management. One estimate for the global market for Electronic Thermal Management is that it will reach $8.6 billion by 2015. For the UK to remain a significant international player in this area there needs to be a strong research base. Our proposal not only provides new knowledge into the physical phenomena of two-phase flow at the micro scale but also direct benefit, in the form of enhanced cooling technologies that can be applied by the industrial partners supporting this proposal.
The proposal will also lead to the training of researchers who can contribute to this area in the future. This includes training in advanced experimental techniques and numerical methods that can be used in a variety of projects/applications. In addition, the immediate interaction with our industrial partners will add direct value to the training of the PDRA and offer both them and the more experienced academics, increased insight into the industrial needs, constraints and avenues for application of state-of-the-art research. Without expertise in adequate cooling technologies, the future growth of microsystems in the UK will be hampered with the danger that innovative designs are shelved through the inability to fabricate cooling systems or that commercialisation takes place outside the UK where cooling solutions are available.
Brunel University London | LEAD_ORG |
Sustainable Engine Systems Ltd | COLLAB_ORG |
Thermacore Europe | COLLAB_ORG |
OXFORD NANOSYSTEMS LTD | COLLAB_ORG |
Rainford Precision Machines | COLLAB_ORG |
Selex ES | COLLAB_ORG |
Leonardo (United Kingdom) | PP_ORG |
Rainford Precision (United Kingdom) | PP_ORG |
Thermacore (United Kingdom) | PP_ORG |
Sustainable Energy Systems (United Kingdom) | PP_ORG |
Tassos Karayiannis | PI_PER |
David Kenning | COI_PER |
Kai Cheng | COI_PER |
Subjects by relevance
- Heat transfer
- Refrigeration
- Heat energy
- Heat exchangers
- Electronics industry
- Refrigeration engineering
- Temperature
Extracted key phrases
- High heat transfer coefficient
- High heat flux
- Heat transfer area
- Micro heat exchanger
- Heat transfer rate
- Local heat flux
- Volume ratio heat exchanger
- Heat pipe
- Heat engine
- Heat source
- Rapid heat
- High thermal load
- Microchannel flow boiling process
- Fundamental fluid flow
- Research development
Related Pages
UK Project Locations
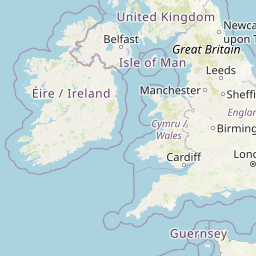
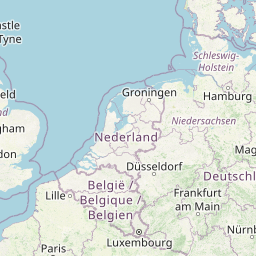
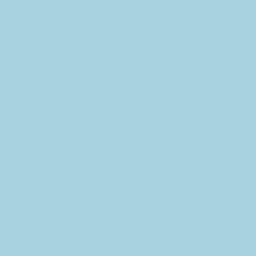
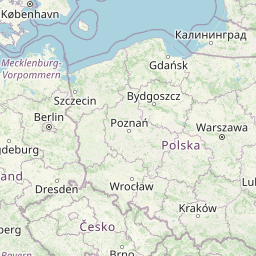





