EMATs for non-contact NDE of austenitic steel
Find Similar History 16 Claim Ownership Request Data Change Add FavouriteTitle
CoPED ID
Status
Value
Start Date
End Date
Description
Power generation and petrochemical plant and civil structures require regular inspection and monitoring to ensure continued safe and reliable operation. The various ways that metal structures are routinely tested includes visual inspection, electromagnetic and radiographic methods and ultrasonic inspection, each technique having its own strengths and weaknesses, often being used in a complementary approach. Of all these methods, ultrasonic inspection is most prolific as it is inherently safe, portable and can be used to detect a wide range of defects down to sub-millimetre sizes. In recent years there has been significant and sustained progress in the fundamental scientific research of guided wave non-destructive evaluation (NDE). The majority of existing guided wave technology uses contacting transducers that must be clamped around the circumference of a pipe in the form of a ring of transducers. Typically a particular mode at a particular frequency is selected with suitable properties for being able to propagate over tens of metres, whilst having sensitivity to defects of interest. Target defect sizes are usually around 25% wall loss or more, which is perfectly acceptable for many applications. Guided waves can be used over shorter distances, and in general there is a trade-off between propagation distance and sensitivity.There is a need to maintain the current power generation plant, particularly within the nuclear industry and with an increase in our reliance on nuclear power anticipated, we need to ensure that we have suitable methods for inspecting critical components. As such, this project focuses on the ultrasonic inspection of stainless steel using ultrasonic transducers called EMATs that can generate or detect ultrasonic waves in metals without being in good mechanical contact with the sample. The advantages of using non-contact methods are that the automation of scanning is easier to implement as contact is not required and the EMATs have a unique set of characteristics that enable them to generate a wide range of wavemodes over a wide range of frequencies, unlike contacting piezoelectric transducers that are usually used at a particular fixed frequency. Note though that EMAT inspection does have some limitations, most principally because they are fairly inefficient when compared to piezoelectric transducers, and so the methods developed in this project are designed to complement the existing technology, providing new inspection capability through fundamental research of the transduction process and the wave propagation in the target sample.To realise fully the potential of EMAT based inspection we need to be able to model the problem scientifically from the bottom up, starting with the shape of the component and the target defect. Target components may be pipes, but will often be components with more complex geometries or problematic material properties as is often the case with stainless steel welds. Modelling how ultrasound propagates through such components can now be reasonably tackled on a high specification desktop PC using methods such as finite element (FE) analysis. Computation time obviously depends on the complexity and size of the model, and the range of frequencies being modelled, but typically one would expect models to take several hours to run on representative components. This needs to be complemented by modelling the behaviour of the transducers, again using FE modelling of the electromagnetic behaviour of sample and transducer. In some cases it is appropriate to combine these FE models with analytical models to improve computation time. Rather than simply providing solutions to a limited number of inspection issues, we will develop a scientific methodology for designing techniques to inspect components of any geometry, equipping both researchers and industrial users with an approach for making the right tool for a specific job rather than providing a limited range of tools.
More Information
Potential Impact:
Industrial beneficiaries include the power generation industry, particularly the nuclear industry where the extensive use of thick sectioned austenitic steel and austenitic welds are challenging for conventional ultrasonic NDT. The petrochemical industry and marine and aviation sectors, will benefit from the provision of novel guided wave approaches to measurement and inspection, as the proposed methods will offers a significant advantage over the currently available techniques. Manufacturers will be able to inspect components more quickly with increased reliability. The pulsed array approach will have applications in radar and sonar, providing a new approach to scanning large volumes simultaneously. The new scientific generated by the project will be of benefit to researchers involved in NDE, materials characterisation and will provide a new way to consider driving and using array based sensors. Automated measurement and inspection is easier to implement when the transduction method is non-contact, whilst new approaches such as the pulsed array technique, have the potential to perform inspection more quickly, with reduced hardware costs. Wavemodes that cannot be easily generated using conventional methods, such as the SH wave mode, have significant benefits for the inspection of austenitic weld microstructures. More generally, ultrasonic measurements can be realised that would not otherwise be performed. Non-contact methods will yield reduced preparation requirements, inspection times and reduced downtime. Improved measurement and inspection leads to increased safety for staff and the public, increases safety of energy supply or process operation with increased plant reliability. Knowledge - the project will deliver new techniques and more generic scientific advances such as the array work Economy - the work will eventually lead to the creation of new transducers and methodologies for NDE, generating inward investment through cost saving and improved safety, creating wealth from the provision of new equipment and services and possibly leading to the formation of new spin-out companies to exploit the technology. Society - plant safety and reliability will improve, easier ways of automating inspections will limit the exposure of staff to hazardous environments. People - the PDRA, PhD students and academic investigators will benefit from training and obtaining new knowledge, as will the industrial collaborators who will have the opportunity to become closely involved with the research, researchers outside the group will also develop new skills through the dissemination activities. We consulted a number of industrial partners in an attempt to define their current and future inspection requirements. We engage with a wide range of industries directly through RCNDE, whose members include the major national power generation and petrochemical industries, and are being financially supported in this project by both Rolls Royce and the Nuclear Decommissioning Authority through the National Nuclear Laboratories. Key findings and progress will be communicated to the wider community outside RCNDE through dissemination in journal publications, at national and international conferences and on a dedicated website. We will have the capability within the research team to not only perform the research tasks, but also the dissemination activities. The industrial collaborators will also assist with dissemination activities, providing us with increased access and guidance on how to better target industrial organisations. There are various exploitation routes available to use including the involvement of the University Technology Transfer Department and links with SMEs and equipment manufacturers and University spin-out companies. A patent application has been made for the pulsed array technique, which may have applications outside ultrasonic measurement.
University of Warwick | LEAD_ORG |
Rolls-Royce (United Kingdom) | PP_ORG |
National Nuclear Laboratory | PP_ORG |
Serco (United Kingdom) | PP_ORG |
Steven Dixon | PI_PER |
Rachel Edwards | COI_PER |
David Hutchins | COI_PER |
Subjects by relevance
- Automation
- Inspection and revision
- Nuclear power plants
- Ultrasound
Extracted key phrases
- New inspection capability
- Emat
- Ultrasonic inspection
- Contact method
- Contact NDE
- Current power generation plant
- Regular inspection
- Future inspection requirement
- Inspection time
- Wave non
- EMAT inspection
- Visual inspection
- Power generation industry
- Inspection issue
- Major national power generation
Related Pages
UK Project Locations
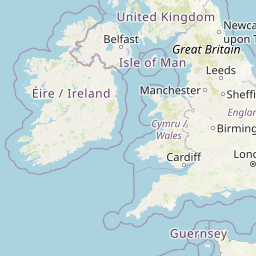
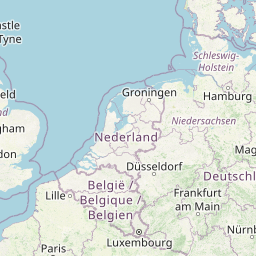
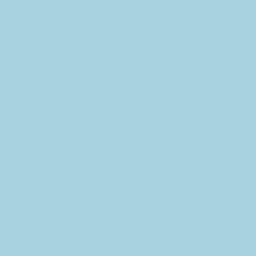
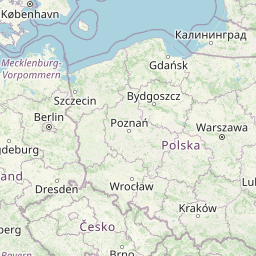



