Decarbonising The Acrylic Value Chain Via Resource Circularity
Find Similar History 23 Claim Ownership Request Data Change Add FavouriteTitle
CoPED ID
Status
Value
Start Date
End Date
Description
The UK has long held a world-leading capability in acrylic technology. UK innovation in acrylic technology started with the world's first commercial production process in the 1930s. The earliest major application of acrylic materials was the substitution of glass with acrylic glazing in British World War II fighter planes, resulting in lighter weight and a significant improvement to pilot survivability when wounded by shrapnel. Lucite's UK presence includes an award-winning technology development capability at the Wilton Research Centre, and world scale manufacturing assets at Billingham and Newton Aycliffe. As durable materials, acrylic polymers have numerous advantageous properties, including excellent optical properties, resistance to weathering, imparting high performance to surface coatings, bio-compatibility, and the opportunity of recycling via depolymerisation. The increasing market size is due to both the heightened demand for acrylic glass and the expanding number of new applications. Given pMMA's versatility, the annual market will exceed $8 billion US dollars by 2025, growing at a rate of 8-9% per year. As demand continues to grow, the need for increased sustainability and fur-ther waste reductions is paramount. In 2012, the International Energy Agency designated meth-acrylic acid as a noteworthy target for the design of sustainable manufacturing [5]. Therefore, an extraordinary opportunity exists to decarbonise this value chain though UK technology leadership spanning the global stage.
The two principal research challenges of the Prosperity Partnership are:
(1) Decarbonise the acrylics value chain through resource circularity.
(2) Maintain and extend the UK's technical and manufacturing leadership in this sector through 21st century manufacturing excellence in the North East of England.
These UK advances in acrylic technology will have both national and global deployment capability, representing a first in class demonstration of decarbonisation through resource circularity in the bulk chemicals sector. This Prosperity Partnership will frame and catalyse further knowledge exchange, given that the anticipated global reduction in carbon intensity aligns with (1) UK legislation on attaining net zero carbon emissions by 2050, (2) the UK's Clean Growth grand challenge and (3) UKRI's Industrial Strategy policy of promoting decarbonisation, catalysing growth via resource circularity and the use of sustainable polymers.
University of Nottingham | LEAD_ORG |
University of St Andrews | COLLAB_ORG |
Mitsubishi Chemical Co Ltd | COLLAB_ORG |
Lucite International (United Kingdom) | PP_ORG |
Alex Conradie | PI_PER |
Jeremy Titman | COI_PER |
Samantha Bryan | COI_PER |
John Robinson | COI_PER |
Jon McKechnie | COI_PER |
Eleanor Binner | COI_PER |
Sharon Ashbrook | COI_PER |
Paul Brian Webb | COI_PER |
Kathleen Haigh | RESEARCH_PER |
Eleanor Binner | PI_PER |
Subjects by relevance
- Sustainable development
- Acryl
- Technology
- Well-being
- Manufacturing
- Acrylic painting
- Polymers
Extracted key phrases
- UK technology leadership
- Acrylic technology
- Acrylic Value Chain
- Decarbonise
- Acrylic material
- Acrylic glass
- Acrylic polymer
- Acrylic glazing
- Acrylic acid
- UK presence
- Technology development capability
- UK legislation
- World scale manufacturing asset
- Resource Circularity
- Global deployment capability
Related Pages
UK Project Locations
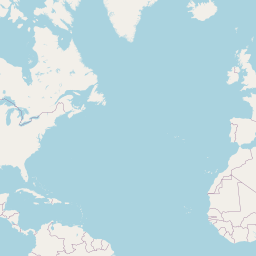

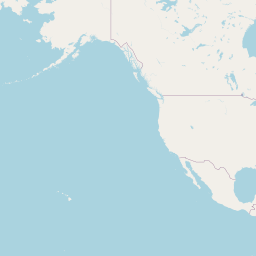
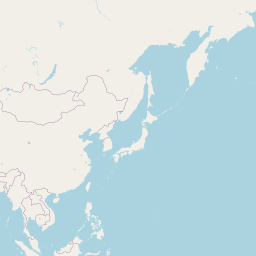
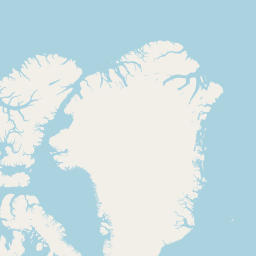
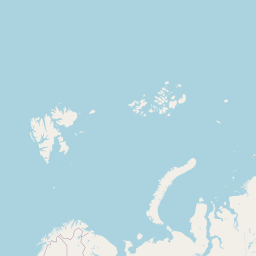
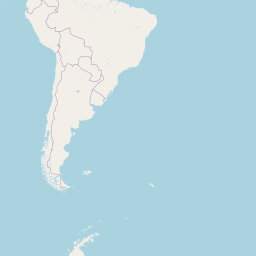
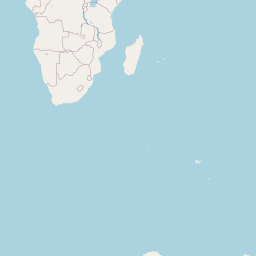
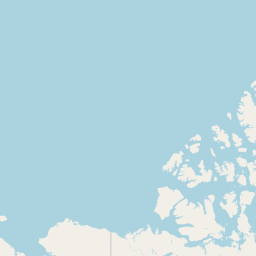
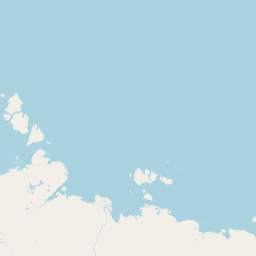
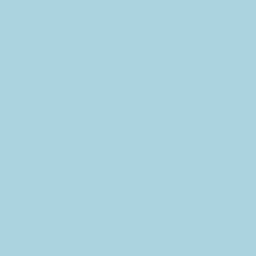
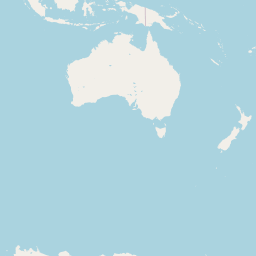
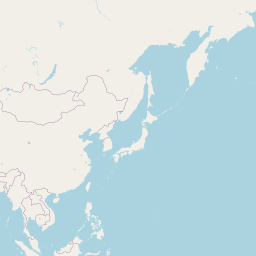
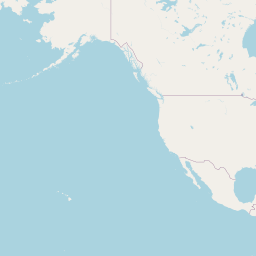
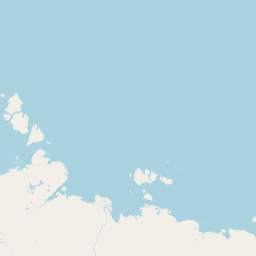
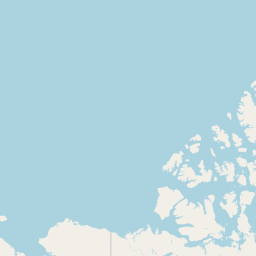
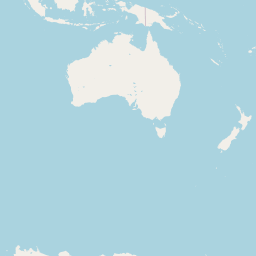
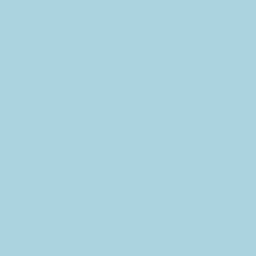

